PLEASE NOTE: the member portal is under maintenance
Frame Corrosion
Corrosion
GALVANIC CORROSION
Corrosion is a natural process that results in the gradual destruction of materials (usually metals) by chemical and/or electrochemical reaction with their environment. Galvanic corrosion is the same process that occurs in a lead-acid battery, electrons move from one metal to another when immersed in a fluid medium (corrosive environment).
A corrosive environment is one where metals are in contact with a fluid that will allow the transfer of electrons. This transfer can take place in plain water, but corrosion will occur more rapidly in water with dissolved salts.
Metals can be classified as either more “Active” or more “Noble”. The more active, the more susceptible that metal is to give up its ions in a corrosive medium. In Galvanic Corrosion electrons flow from the more active metal “anode” to the more noble metal (cathode). It is for this reason that we add an anode to a water pump. The anode is made from a metal that is more active than the cast iron of the pump casing. The anode corrodes over time instead of the cast iron, protecting the pump components. Once the active metal in the anode has been used up it must be replaced to continue the protection.
GALVANIC CORROSION (Continued)
The following table shows a list of metals and their relative “activity”. Notice the relative position of steel and copper on the chart. The steel is more active, so in a corrosive environment with copper, the steel will corrode.
GALVANIC CORROSION (Continued)
The protective action of the more active metal can be seen when a steel nut is used with a copper bolt. In this case the steel nut rusts, and the copper bolt is pristine. The reverse occurs when a copper nut is used with a steel bolt.
The more dissimilar the metals (the farther away from one another they are on the galvanic chart) the greater the corrosion potential will be.
GENERAL UNIFORM CORROSION
Uniform corrosion is defined as a type of corrosion attack (deterioration) that is more or less uniformly distributed over the entire exposed surface of a metal. It happens in the presence of oxygen. The oxygen can be in air or in water. Steel turns to iron oxide (red scale), and aluminum turns to aluminum oxide (white or grey powder).
LOCALIZED CORROSION
Localized corrosion is defined as the selective removal of metal by corrosion at small areas or zones on a metal surface in contact with a corrosive environment, usually a liquid. It usually takes place when small local sites are attacked at a much higher rate than the rest of the original surface.
Contents
Corrosion from Road Chemicals
There are a range of chemicals used by highway departments to melt ice in winter weather. The addition of these chemicals to ice lowers the melting point, helping to turn the ice to a liquid at a temperature lower than the normal freezing temperature. Unfortunately, salt solutions also act to greatly increase galvanic corrosion on truck frames and components.
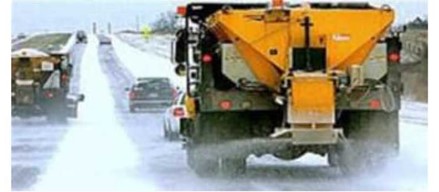
SODIUM CHLORIDE
In the past the only chemical commonly used as a deicer was sodium chloride (common rock salt or table salt). Sodium chloride is also known as the mineral halite. When mixed into water, the resulting salt solution acts as a super electrolyte, allowing electrons to flow through the solution more readily, speeding up electron transfer between dissimilar metals and thereby increasing the rate of galvanic corrosion.
MAGNESIUM CHLORIDE
Magnesium chloride is the name for the chemical compound MgCl2 and its various hydrates. Magnesium chloride is highly soluble in water and will lower the melting point of water more than will rock salt. The better melting ability of magnesium chloride prevents the ice bond, allowing snowplows to clear the roads more efficiently.
CALCIUM CHLORIDE
Calcium chloride is an inorganic compound, a salt with the chemical formula CaCl2. It is a colorless crystalline solid at room temperature, highly soluble in water. In the first 20 minutes after application at 20°F (-7°C), Calcium Chloride Pellets melt approximately twice as much ice as an equal amount of rock salt.
While most other deicers depend on their surroundings for heat, Calcium Chloride actually generates heat as it dissolves to form ice melting brine. A pound of calcium chloride can raise the temperature of a gallon of water by over 30°F (17°C). This heat release is especially important during cold weather when other deicers lose effectiveness.
WORSE THAN ROCK SALT
Magnesium Chloride and Calcium Chloride solutions wick into cervices and cause galvanic corrosion until the water in the solution evaporates. Once dry they remain on surfaces, reactivating with any addition of new moisture from rain, dew, or even just high levels of humidity in the air.
New Apparatus Options to Prevent Corrosion
GALVANIZING
The single most important thing that you can do to prevent a frame corrosion problem on a new order is to specify galvanized frames and frame components.
Hot dip galvanizing has been utilized for over 250 years to protect steel and iron from the destruction of corrosion. Hot-dip galvanizing is the process of immersing iron or steel in a bath of molten zinc. While the steel is immersed in the zinc, a metallurgical reaction occurs between the iron in the steel and the molten zinc. This reaction is a diffusion process, so the coating forms perpendicular to all surfaces creating a uniform thickness throughout the part.
The galvanizing kettle (Figure 5) is heated to a temperature ranging from 820-860 F (438-460 C), at which point the zinc is in a liquid state. The steel will stay in the bath until the steel heats to the bath temperature. Once the diffusion reaction of iron and zinc is complete, the steel product is withdrawn from the zinc kettle.
When exposed to the atmosphere, the pure zinc (Zn) reacts with oxygen (O2) to form zinc oxide (ZnO), which further reacts with carbon dioxide (CO2) to form zinc carbonate (ZnCO3).
GALVANIZING WITH TOPCOAT
Top coatings can be applied directly over the galvanized surface, but there are special processes and timing that is required to do so. The addition of a topcoat over a galvanized surface may be more costly that a topcoat by itself because of the added logistics involved.
POLYUREA COATINGS
Polyurea is an organic polymer that forms plastic-like or rubber-like compound that may be used on many surfaces (i.e., bedliner coatings). Departments requiring corrosion-, abrasion-, and impact-resistant coatings on tread plate walking surfaces and other areas are turning to these spray-on textured coatings. They can also be used to treat frames and undercarriage components.
Failure to keep your frame assembly clean, particularly during the winter months where they are exposed to de-icing chemicals can void a warranty and lead to very expensive refurbishment bills. This is just as important for departments close to the ocean as airborne sea salt can be just as damaging as rust-belt road salts.
Regular Cleaning Guidelines
The best way to minimize frame corrosion damage is to keep the undercarriage clean. This should be done after each weather event where de-icing agents are employed, and at least every 10 days during the winter months in regions where there are de-icing agents on the roads. Clean regularly all season long if your department is close to the ocean.
For proper cleaning you will need
- Means to get the apparatus off the ground
- Pressure washer
- Source of warm water
- Mild detergent
- Appropriate PPE
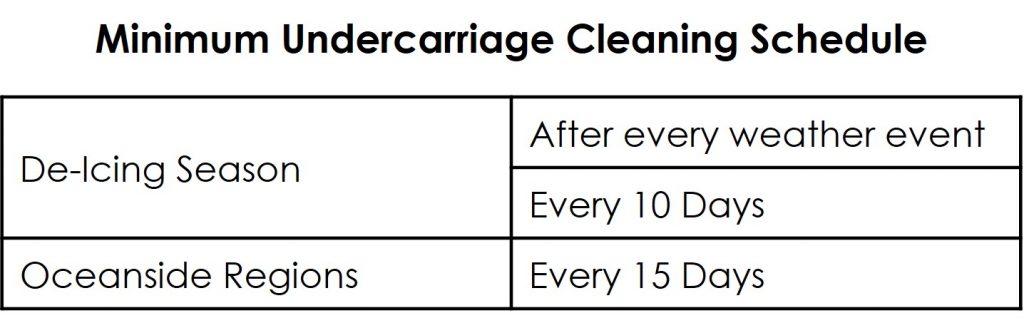
IMPORTANCE OF CLEANING
Frame rails assemblies are very susceptible to the attack from road chemicals for several reasons. Frames are at the bottom of a truck and exposed to road spray. The necessary attachment of crossmembers, body supports, and other components create crevices where chemicals and moisture can penetrate. The use of double or triple frames also creates small gaps between the liners where corrosion can form. Finally, the fact that the frame assembly is hidden beneath the truck means that dirt and chemicals are hidden from view and therefore often overlooked during the cleaning process.
GALVANIZED SURFACES
Galvanizing is not a cure-all for corrosion and a galvanized frame must still be kept free of road de-icing agents. Galvanized surfaces exposed to de-icing slush has been found to “melt” the zinc right off the rails. Remove de-icing slush from galvanized surfaces promptly.
PPE
Before working under your apparatus be sure you are equipped with the appropriate Personal Protective Equipment as directed by your department SOPs and industry best practices. At a minimum you should be wearing safety goggles prior to using the pressure washer or compressed air wand.
UNDERCARRIAGE FLUSHING
Lift the apparatus using all the necessary safety procedures and a set of truck hoists. Working from the front to the back follow these steps:
- Initial Rinse
- This first rinse will wet the surfaces and remove heavy build-up of contaminants.
- Soap-Water Wash
- Application of a mild detergent will help to break up the dirt
- Final Rinse
- Comprehensive clean water flush
Avoid spraying directly on electronics and electrical connections. Pay special attention to:
- Areas where heavy brackets such as suspension and steering components are bolted to the frame.
- Crevices between major components and the frame such as aerial torque boxes, water tanks, and body structures.
- Gaps between frame rails and liners
- Attachment areas between frame rails and crossmembers
This process may dislodge loose paint or other coatings. This is a good thing since the gaps under peeling paint can trap water and chemicals and speed up the corrosion process.
Inspect the undercarriage after cleaning thoroughly to ensure that all corrosive chemicals have been washed away.
DRYING
Once the undercarriage is clean it needs to be dry. The drying process can be sped up by using a compressed air wand or an electric leaf blower to blow the water out of all the crevices and areas that you have just washed. This process may dislodge further peeling paint or dirt. Keep your goggles on.
WATER DISPLACEMENT
Use a water displacing solvent such as WD-40 to treat all the areas around the spots that you have cleaned and dried. The WD in WD-40 stands for “Water Displacing”. While we all may use it as a lubricant, the original use was to prevent corrosion on Atlas Missiles. A water displacing formula will wick into the cracks and gaps to force out any remaining moisture and help prevent moisture from making its way back in. Don’t be shy to use a couple of cans at a time. It is cheap insurance and will more than pay back the investment long term.
Note: Avoid applying lubricants to brake friction surfaces such as brake rotors, drums pads or shoes. Avoid spraying solvents on critical plastic parts that may react with them.
INSPECT FOR SERIOUS DAMAGE
During each undercarriage treatment be sure to watch for signs of significant damage. Make note of areas where paint is missing, and the apparatus needs further repair. Schedule the apparatus for preventive maintenance at the next opportunity.
REGULAR CLEANING
While not a substitute for the monthly cleaning, a very good practice is to flush the undercarriage every time it is washed. It may not be practical to raise the apparatus into the air for each washing so you may wish to consider an undercarriage washing system. This may be available at certain truck wash centers, or you can create your own as did the Waukee Fire Department.
Protective Coating Repairs
For any areas where the protective coating has been significantly damaged or signs of corrosion has begun, it is important to treat and re-protect the area promptly. This should be conducted trained professionals and will involve the following steps.
CLEANING
The undercarriage should be cleaned and dried as described above.
SANDING OR BLASTING
Corroded areas need to be treated by either sanding or blasting to remove all active byproducts of corrosion (rust). Sand or bead blasting is preferred as this will do a better job of knocking the rust out of pits or inclusions. Be sure to protect sensitive components such as electronics, electrical harnesses and connections, hydraulic hoses, brake components, etc.
BASE COATING
The treated areas must now be protected to prevent further corrosion. This should begin with a rust-preventative primer followed by a hard finish coat. Allow these coatings to dry thoroughly and to “flash off” before applying a protective coating.
UNDERCOATING
Once the damaged areas have been painted, apply a protective coating over the top. This can be any of the following:
Soft Film Barriers such as a spray-on or brush-on under coating. This type of coating will typically remain soft and pliable.
OIL FILM BARRIER
Oils and greases on metal surfaces can be an effective means of protecting.
POLYUREA COATING
Bedliner or Polyurea coating is a good way to protect painted surfaces from the physical damage due to road debris that can later lead to chemical attack.
Frame Damage Assessment
If frame damage goes unaddressed it will eventually get to the point where the apparatus loses structural integrity. At this point the damage will need to be repaired, or the frame rails replaced. The following steps can be taken to determine which approach is appropriate.
PRE-INSPECTION CLEANING.
The first step in assessment is to perform the cleaning and sanding or blasting steps described earlier. This will reveal the base material and allow the assessor to measure the corrosion damage.
MEASURING DAMAGE
If both sides of the damaged material are accessible, the remaining thickness can be measured using a caliper or micrometer. For areas where both sides cannot be accessed, measure the thickness with an ultrasonic measuring device.
Compare the thickness in the damaged area to an undamaged section of frame, or to the original specifications. If using the original specifications, be sure you are referencing the actual engineering specifications, not the sales data which is typically stated in terms of a nominal thickness.
Determine the percentage of lost material by comparing the damaged area thickness to the original thickness using the following formula:
Original Thickness: OT
Damaged Thickness: DT
Percent Loss = (OT-DT)/OT.
If the apparatus frame has a liner or double liner, then the Percent Loss is calculated using the total of all thicknesses:
Percent Loss= (OT Frame + OT Liner – DT Frame -DT Liner)/(OT Frame + OT Liner)
Frame Repair Guidelines
DAMAGE CRITERIA
As a rule of thumb, any area where the Percent Loss is less than 33% can be cleaned up and protected using the methods described in this document. Damage greater than 33% should be repaired as follows.
FLANGE DAMAGE
Areas of the flange where the percent loss is greater than 33% should be reinforced with a fishplate appropriately bolted to the web of the base frame material and extending at least 6 inches beyond where the 33% or greater damage has ended. The fishplate should have a flange at least as wide as the original frame flange resting as close as practicable to the damaged flange.
WEB DAMAGE
Areas of the web where the percent loss is greater than 33% should be reinforced with a fishplate appropriately bolted to the web of the base frame material and extending at least 6 inches beyond where the 33% or greater damage has ended. The fishplate does not need to include a flange as long as the connecting bolts can be spaced in sound material above and below the damaged area. If the damaged area extends into the flange radius, then the fishplate should include a flange as well.
If there are local areas of damaged material deeper than 33% but no larger than 2 inch in diameter these can be treated without fish-plating as long as they are no closer than half their diameter to the flange.
FISH-PLATE MATERIAL
Fish-plates should be fabricated from the same material as the frame rails, or from an alternate material recommended by the chassis OEM.
OEM ADVICE
Where frame damage is extensive it is advisable to contact your OEM for review. They will need good photos and measurements of the damage. They may consider the extent of the damage in relation to the expected stress in the damaged area and provide guidance on whether the damage is repairable or if the frame will need to be replaced.