Wildland Apparatus
INTRODUCTION
Wildland fire apparatus are essential in jurisdictions that contain undeveloped land areas susceptible to natural fuel fires – aka wildfires, brush fires, grass fires, forest fires, field fires, and the like. These areas often have different challenges for fire suppression than more developed areas – limited water supplies, reduced accessibility to the fire, increased response times and distances, widespread combustible ground cover, and the potential for rapid fire spread across a wide front. Fire departments responding in these areas require wildland apparatus designed with these conditions in mind (Figure 1). Often such rigs are smaller to account for the reduced accessibility and are equipped with all wheel drive and higher ground clearance for off-road travel. Brush guards or similar protection may be installed to prevent damage to the unit while pushing through ground cover. They are designed to carry “just enough” water to balance maneuverability and fire suppression, but the pumps are frequently lower volume / higher pressure to maximize the effectiveness of what they do carry. And because such fires are rarely stationary, the apparatus must be able to move quickly and reposition during attack – i.e. pump-and-roll. This document will cover those types of features.
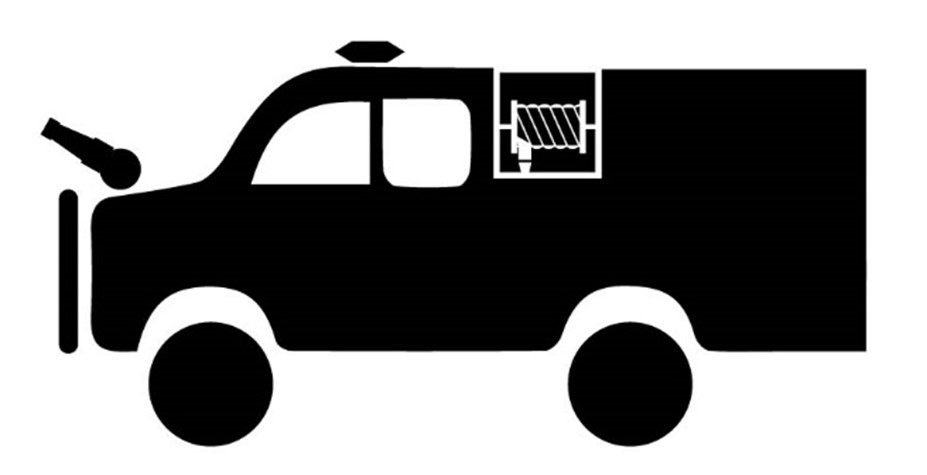
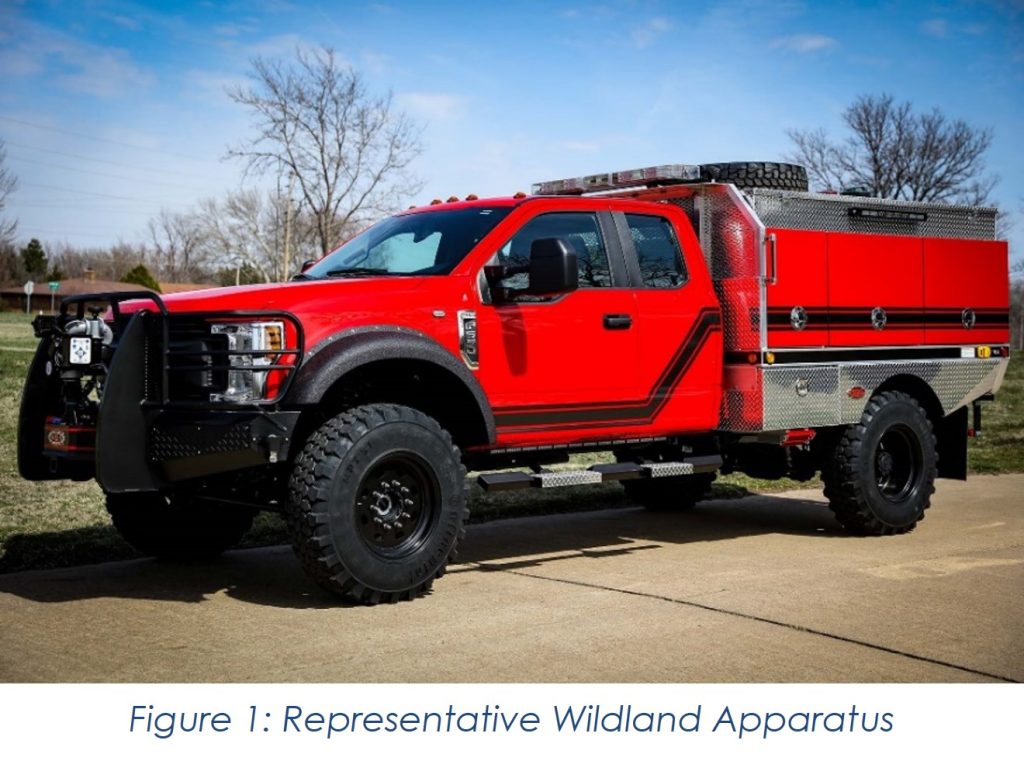
Contents
INTRODUCTION (Continued)
The situation becomes even more specialized where businesses and homes may purposefully encroach into these undeveloped areas, collectively known as the wildland interface zone. Builders in these areas often purposefully try to preserve the natural feel of the surrounding landscape. As such, fires that begin as natural fuel fires may easily spread into adjacent structures and neighborhoods. Fire apparatus responding in these areas must still deal with the challenges of the natural fuel fires, but they must also be able to conduct structural suppression and exposure protection. In addition to the wildland features described above, apparatus designed for these areas may have larger pumps for structural fires, larger water tanks, and other features more typically associated with structural fire apparatus (Figure 2). These apparatus often receive the additional descriptor “Wildland Interface” fire apparatus.
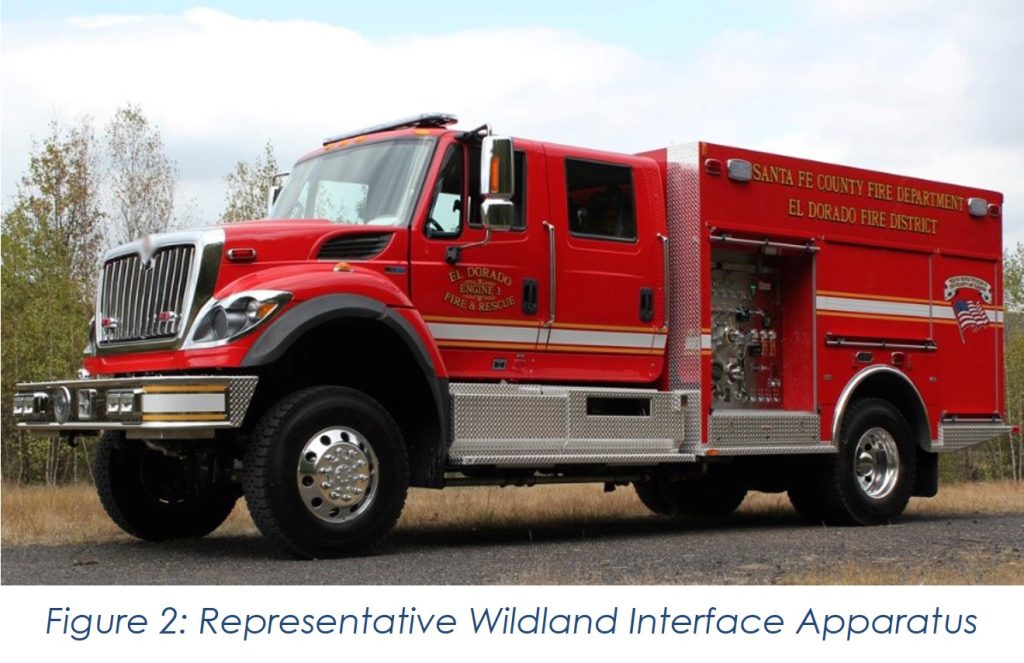
INTRODUCTION (Continued)
Within the US and Canada, there are several dedicated wildland fire agencies that focus almost exclusively on wildland fire suppression. These agencies are at the state and federal level as part of larger land management organizations, Examples include the USDA Forest Service, the US Department of the Interior, and multiple state level forestry departments. With some exceptions, these agencies do not generally provide all-hazard response and primarily protect the tens of thousands of acres under their responsibility. These agencies have two things worth considering in wildland apparatus design. First, because wildland firefighting is their primary mission, they have developed specialized apparatus for their fleets with features and benefits that might be useful to other responders (Figure 3). Second, these are the agencies that manage the major state and national wildland responses. These large fires get national attention and require assistance from many agencies at many levels across a wide geographic area. In order to coordinate the interoperability of all these responders, these agencies set minimum performance standards apparatus must meet to assist on the fire and get reimbursed for their efforts.
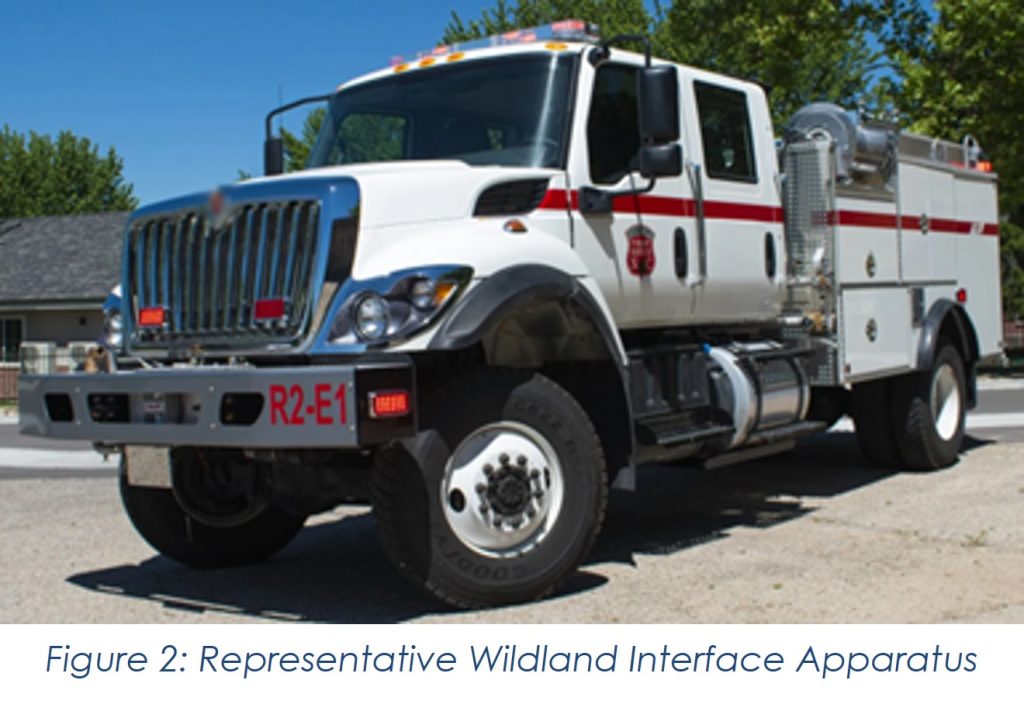
INTRODUCTION (Continued)
Lastly, not every fire department has a year-round wildfire risk, and not every department can afford to have a single-purpose wildland apparatus with limited use. However, the features built into a wildland apparatus that make it useful for accessing harder-to-reach areas will also make it useful during weather events and other natural disasters like snowstorms or hurricanes. To that end, many departments compromise by combining the functions of a wildland apparatus with that of other types of apparatus such as a light rescue or a pumper (Figure 4). Purchasers of these types of apparatus need to balance the competing demands of the different purposes for which the apparatus may be used. For example, having storage space to carry a large complement of rescue equipment will make the apparatus larger and heavier, which may make it less useful off-road. Though such apparatus are not uncommon, this document will cover some of the tradeoffs.
WILDLAND APPARATUS USAGE
There are two key design cases to consider for a wildland apparatus. The first is that the vehicle must be capable of traveling off-road. The severity of the travel will vary with geography, from simple unpaved roads to severe “jeep” trails to true off-road travel through brush and other ground cover. The common ingredient, however, is that the unit – body and chassis – can expect to see a lot of twist. Think of it this way – the wheels will not be on level ground, and the tires will lift and drop by varying amounts. When one corner goes up and one corner stays down, that introduces a twist through the suspension into the chassis frame and ultimately into the body, cab, and water tank. The magnitude of the twist will vary, but you can expect that over the life of the vehicle, the number and magnitude of the twist cycles may exceed typical on-road fire apparatus.
Significant attention should be paid to specifying a wildland apparatus that has a flexibly mounted body that is robust in nature. Body mainframe assemblies that mirror an ARRF or military body application can be the norm. Compartmentation must be designed to allow for severe stress loading, even though the amount of usage compared to other apparatus may be low. Pumps and modules should have special mounts that help reduce vibration and stress loading often seen during off-road use.
Ironically, some Wildland Apparatus also have significant on-highway mileage, particularly if they provide interagency support at major incidents. In some cases, these apparatus will respond hundreds of miles just to get to the scene. For all-wheel drive apparatus, highway miles are not necessarily a blessing. High transmission, transfer case, and axle temperatures can cripple these rigs, especially when traveling in the hot summer months, or in mountainous terrain. Well-designed systems will include dedicated cooling systems, better tires, and unblocked air flow under the chassis. Pay attention to the operational history of similar rigs in similar geography.
The second design consideration is stability and rollover avoidance. Again, the details vary with geography, but there are several factors in off-road use that increase the risk of rollover. These include narrower roads with steeper drop offs, softer shoulders (if the road even has shoulders), rural travel, and loose sand and gravel road surfaces. This is magnified by the risks common to all fire apparatus such as liquid loading and the need for quick response. Therefore, good designs will try to minimize the center of gravity by limiting the water tank size and height. The NFPA standard acknowledges this risk by requiring better stability for wildland apparatus compared with structural apparatus. The tilt table requirements are 26.5° for structural versus 27° or 30° for wildland depending on size. (NFPA 1900 section 7.14.3).
The tendency over the years has been for fire apparatus to grow larger due to chassis horsepower increases, expanding emissions regulations, more personnel being carried, compartmentation needs expanding, and hose and water loads growing. These are particularly detrimental in the wildland apparatus world. When specifying a wildland apparatus, attention should be paid to both the expected tactical use and the environment the apparatus will be operating in. An analysis of the overall acceptable maximum size and weight limitations should be completed prior to design. Failure to follow this will result in an apparatus that will not perform off road when needed because it is too big, too heavy, or simply not designed for the expected environment.
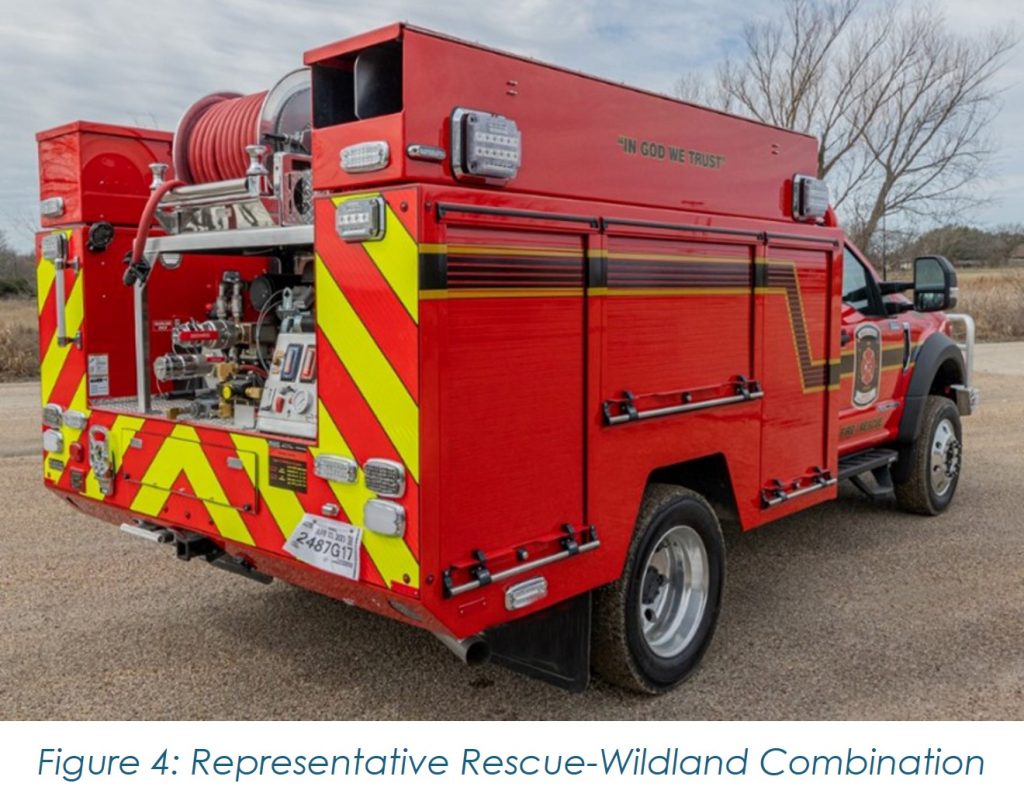
WILDLAND APPARATUS TYPING
There are two documents that should be referenced for wildland apparatus design. The first is NFPA 1900 – Standard for Aircraft Rescue and Firefighting Vehicles, Automotive Fire Apparatus, Wildland Fire Apparatus, and Automotive Ambulances. This standard replaced NFPA 1906 – Standard for Wildland Fire Apparatus in 2023 and incorporated all apparatus requirements into a single publication. The second is the National Wildfire Coordinating Group (NWCG) Water Handling Equipment Guide, PMS 447-1. The National Wildfire Coordinating Group is a consortium of federal and state agencies that establish national interagency wildland fire operations standards. If an individual department supports federal or state managed interagency operations, then compliance with NWCG will be required to be dispatched as an operational asset and to be reimbursed for incurred expenses.
The key portion of the NWCG standard is the apparatus typing standard. This allows incident commanders to quickly request specific apparatus and know what the high-level capabilities of those apparatus will be. These classifications are performance based and not particularly detailed. They simply list the major characteristics of the apparatus including tank size, pump flow and pressure, hose capacity, ladders (if applicable), pump-and-roll capability, crew size, and the maximum GVWR (for some types). The guide may be found at the NWCG website: www.NWCG.gov/publications/447-1.
Because the typing system only focuses on the minimum requirements in each classification, there is a lot of flexibility in configuring apparatus to a specific department’s wants and needs. Apparatus may be decked out with “bells-and-whistles,” or they may be utilitarian style configurations with basic bodies and few extras. If the unit complies with NFPA and is in good working order, then everything else is at the discretion of the purchaser and the builder.
The NWCG typing system is not associated with NFPA. NFPA 1900 provides much more system level detail than the NWCG standard but provides less guidance as to how the apparatus should be built to meet its purpose. For example, it provides details about how a water tank is to be constructed including material and baffling requirements, but it does not recommend how large the water tank should be. Please note that the NFPA 1900 standard only applies to vehicles with a GVWR exceeding 10,000 lbs.
Lastly, it is not uncommon for departments to purchase pickup trucks or offroad recreational type vehicles such as ATV’s and UTV’s for conversion to wildland fire apparatus. It is also not uncommon for departments to build on surplus military vehicles. However, there are limited resources available to use as a nationally recognized standard in these types of conversions. In such cases, it may be possible to refer to NFPA 1900 for certain components, but it will be difficult to fully comply with the standard in all respects. Good engineering principles must apply – make sure the chassis is in good working order, do not overload the unit per the manufacturer’s specifications, and keep the center of gravity below the chassis manufacturer’s requirements.
LARGE WILDLAND ENGINES
For purposes of simplicity, wildland apparatus may be divided into two categories, large and small.
NWCG type 1, 2, 3, and 4 are typically seen as large apparatus. Type 1 and 2 apparatus are specifically designated as structural apparatus (Figure 5). These are the apparatus normally built to what was formerly NFPA 1901. They may or may not have specialized wildland firefighting features such as pump-and-roll or all-wheel drive. But they will always have structural capabilities including a large hose load and a structural ladder complement. Functionally, there is little difference between a type 1 and 2 apparatus. The differences are the minimum size of the pump, the size of the hose load, and the requirement for a master stream device on a type 1.
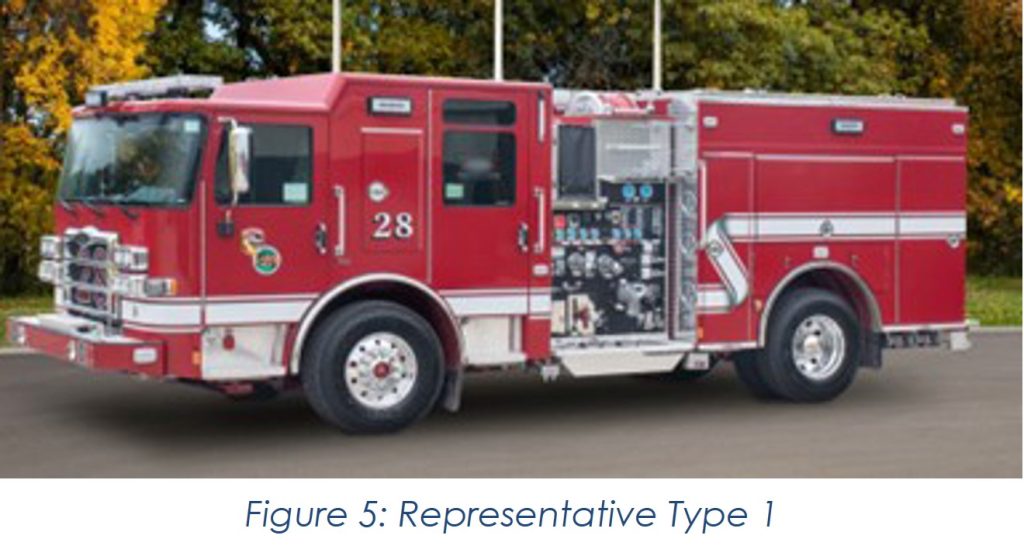
LARGE WILDLAND ENGINES (Continued)
Type 3 and 4 apparatus are more purpose built for wildland response, though they may have some multipurpose capabilities as well. Type 3 units have at least a 500-gallon tank, a 150 gpm @ 250 psi pump capacity, and seating for 3 (Figure 6). Due to the crew size, type 3 apparatus usually have 4 door crew cabs. Type 4 apparatus have a larger tank (minimum 750 gallon), a smaller pump (minimum 50 gpm @ 100 psi), and seating for at least 2 (Figure 7). Both types must have pump and roll. In all cases, the NWCG standards are minimum standards. It is common for the apparatus to exceed the NWCG requirements in one or more categories.
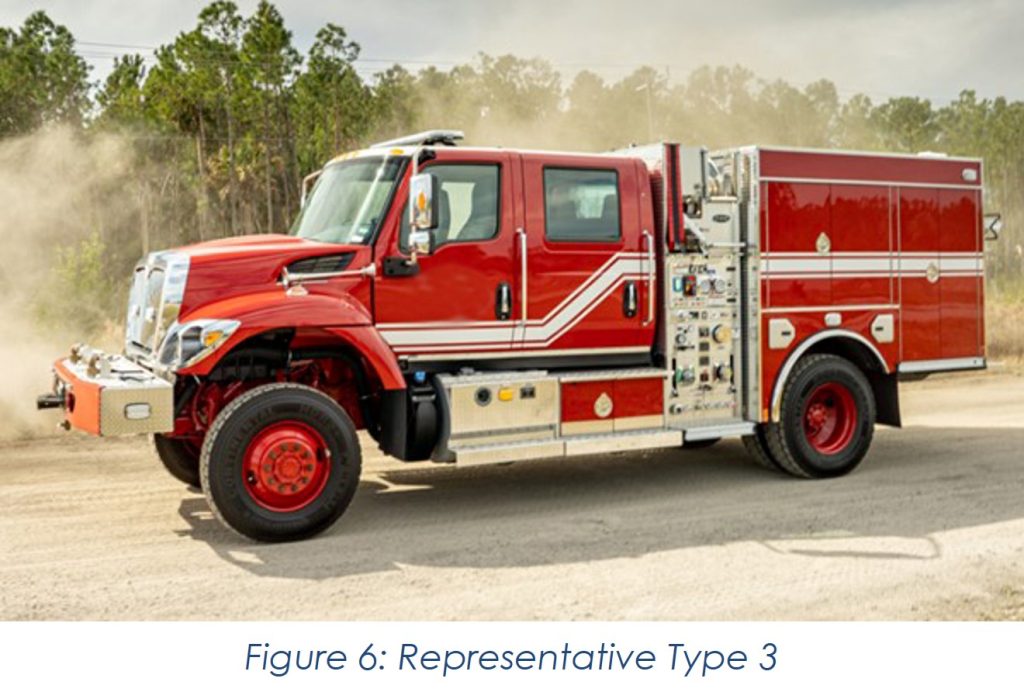
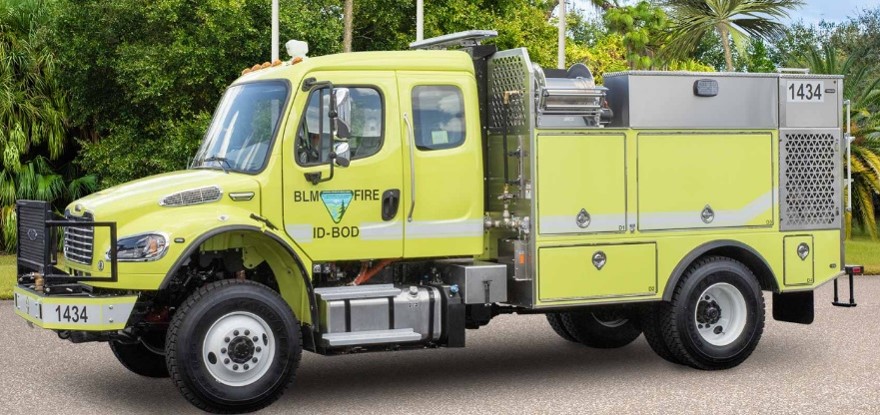
LARGE WILDLAND ENGINES (Continued)
Due to the costs of such units, some departments find it difficult to afford a truck of this size dedicated only to wildland response. In such cases, they may try to justify the purchase by making it as multipurpose as possible – including trying to get full credit as an engine company. Certainly, apparatus have been built that function reasonably well in this role. The tradeoff is that the unit should meet both the wildland and structural requirements of NFPA 1900, including the specified structural equipment allowance, storage for the designated equipment such as ladders, and full structural style pumping systems. Purchasers can expect such apparatus to be longer, taller, and heavier and should be sure the final product will still be functional for their response area.
With a handful of exceptions, most dedicated large wildland apparatus are mounted on engine-forward commercial chassis instead of custom-built fire apparatus chassis. The advantages for each are as follows:
Commercial Chassis (Figure 8):
Advantages: Lower cost (typically), factory installed 4×4 readily available, larger network of product support (typically)
Custom Chassis (Figure 9):
Advantages: Cabover design provides a shorter wheelbase and overall length, more flexible crew seating arrangements, higher cab strength (typically)
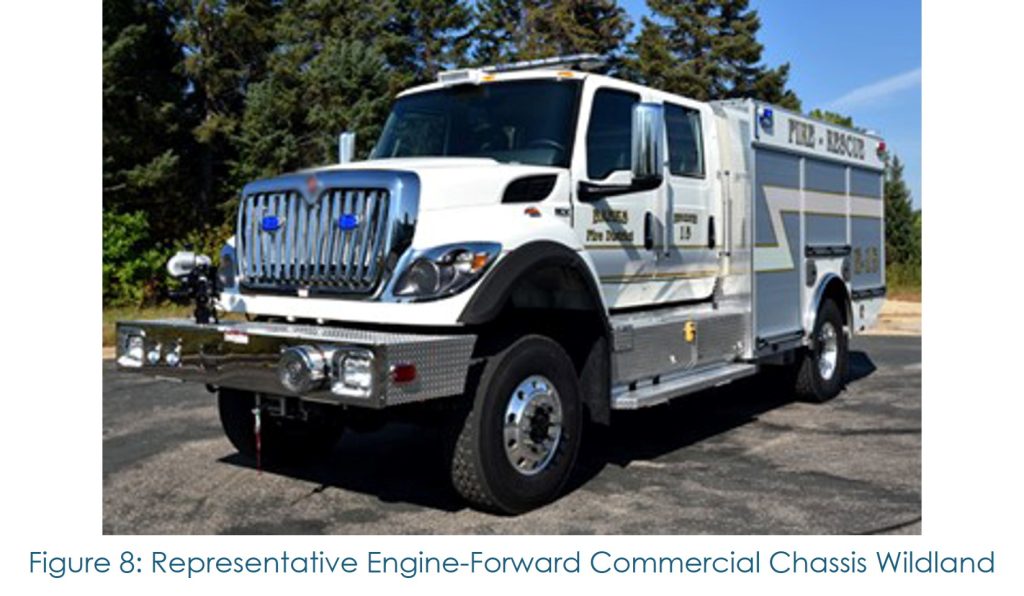
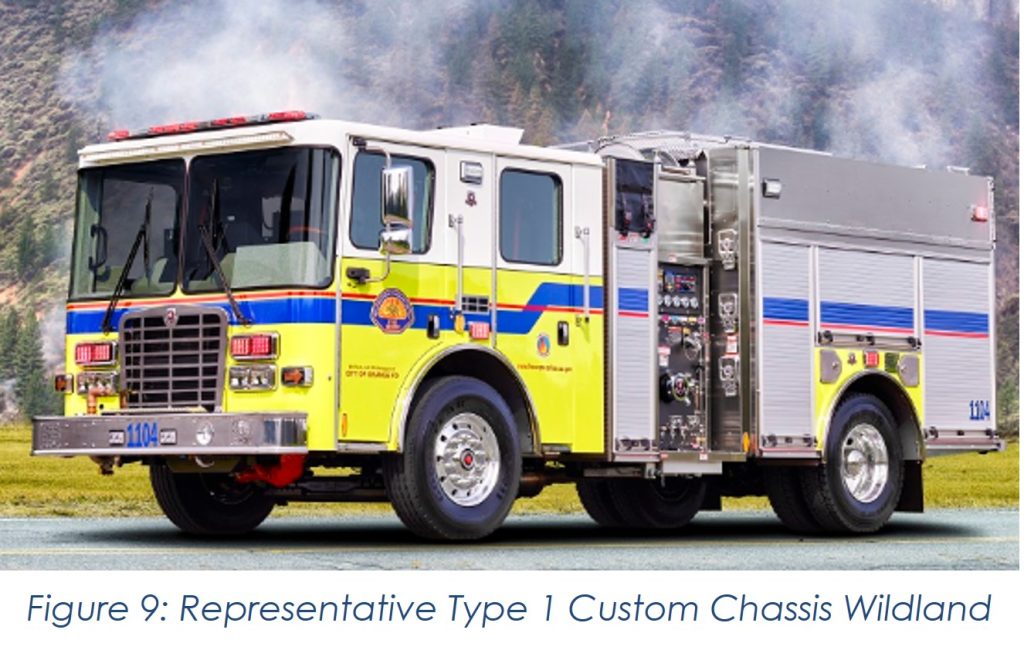
SMALL WILDLAND ENGINES
NWCG type 5, 6, and 7 apparatus are considered small apparatus. The maximum GVWR will be 26,000 lbs for a type 5, and it will decrease from there by type. In appearance, these units will often look like utility trucks or pickup trucks.
Type 7 units are pickup truck size units or smaller (Figure 10). The maximum GVWR is only 14,000 lbs, so the payload capacities are quite limited. These units are only required to have a 50-gallon water tank, and the pump is almost always a small separate engine driven pump. In the federal government typing system, these units are usually designed as patrol units – they access the scene early to hopefully make a stop while the fire is small. In rural, volunteer departments, pickup style units are common due to their small size and cost.
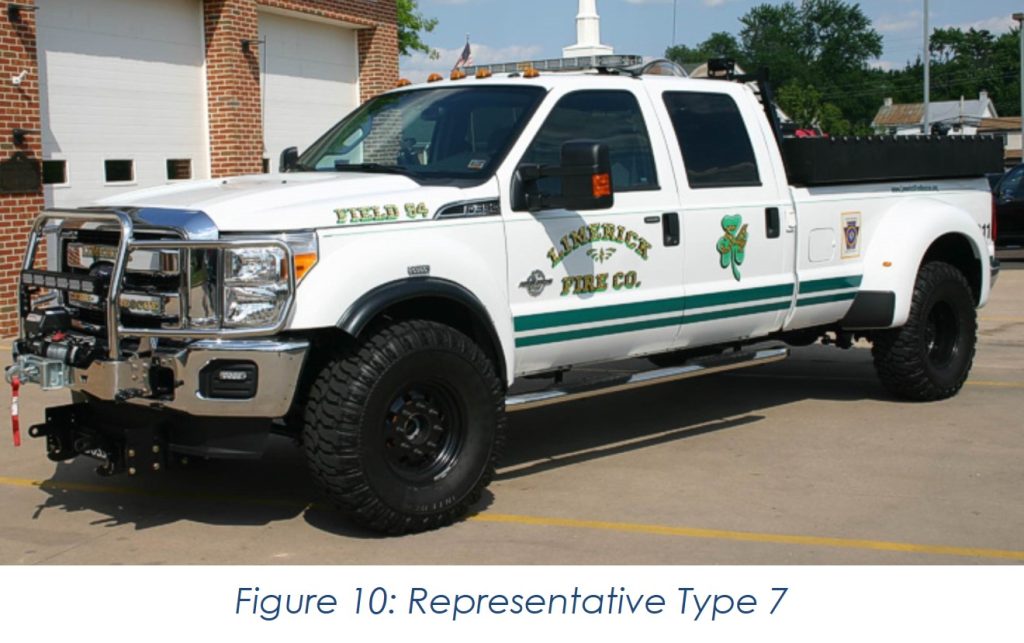
SMALL WILDLAND ENGINES (Continued)
Type 6 apparatus have traditionally been the bread-and-butter vehicles for the wildland apparatus fleet. These units are slightly larger than a pickup, often with a contractor’s style utility body, flatbed body, or light rescue body (Figure 11). The required tank size is only 150 gallons, but in practice 300 gallons is common. The minimum pump size is only 50 gpm @ 100 psi. Typically, this will be a separate engine driven model, and larger flow ratings are possible. As with the Type 3 units, these units are often configured as multi-purpose units – usually light rescues or quick attacks. As with the Type 3 units, the tradeoff is that as more space is dedicated to rescue tools, patient handling equipment, larger structural pumps, etc – the vehicle gets larger.
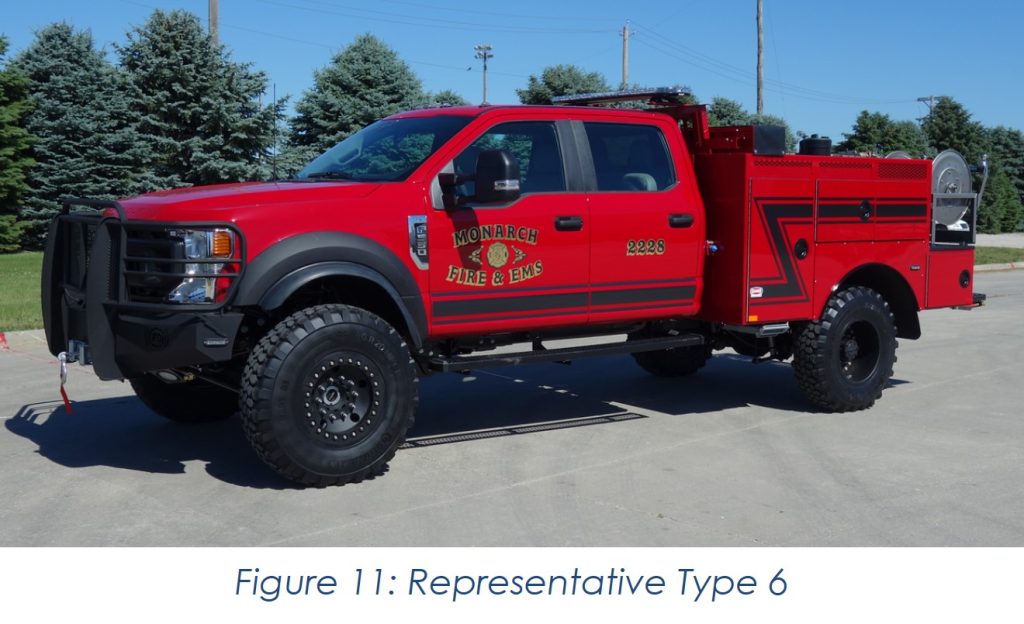
SMALL WILDLAND ENGINES (Continued)
Type 5 units have a maximum GVWR of 26,000 lbs and also require a 400-gallon water tank (Figure 12). In the recent past, there were limited all-wheel drive chassis that would fit this requirement. However, recent changes in commercial chassis offerings combined with new body configurations have renewed interest in this size vehicle. They can be designed to be well under 25’ in length with a height of less than 9’ (4×4), and a weight less than 19,500 lbs loaded. The pump is only required to be 50 gpm @ 100 psi, but like the type 6, larger engine driven pumps are common.
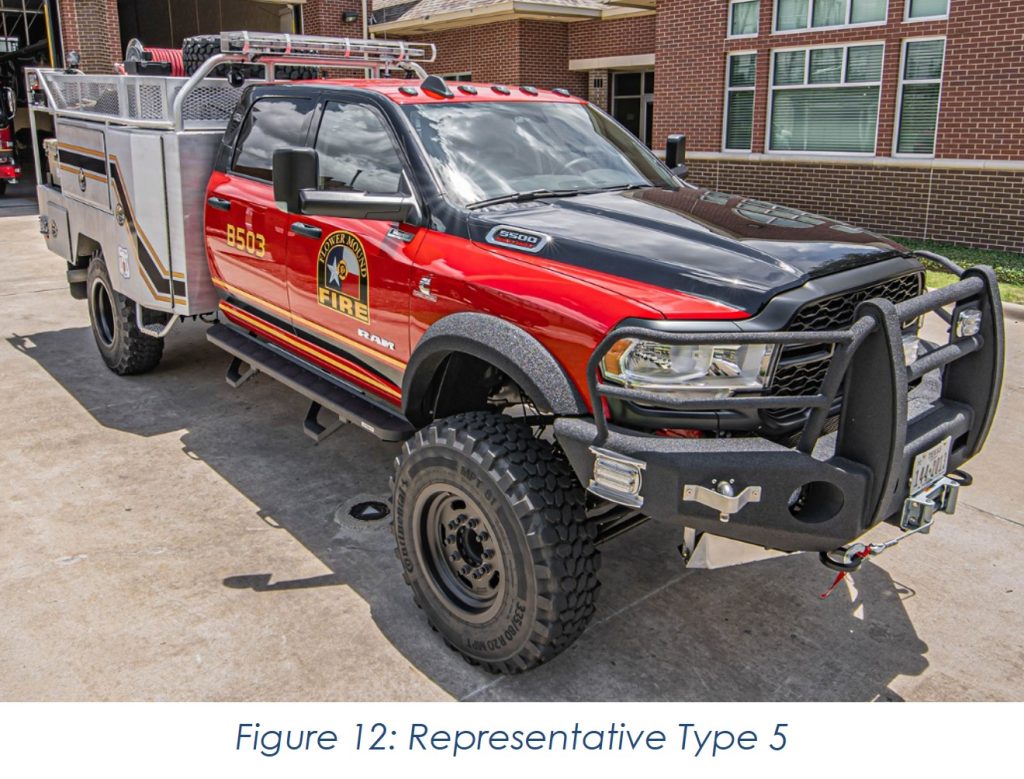
SMALL WILDLAND ENGINES (Continued)
For all small wildland apparatus, the Achilles’ heel is the weight. These units are mounted on commercially available chassis with limited GVWR options. To add confusion, the manufacturers of these chassis rate them differently than larger vehicles in that the total GVWR is often less than the sum of the axle GAWR’s. For example, in one commonly used chassis, the front axle may be rated at 8,000 lbs, and the rear axle may be rated at 14,700 lbs, but the full vehicle is only rated at 19,500 lbs. An in-service apparatus may be overweight in total without overloading either axle.
As a result, it is very easy to overload this type of apparatus without planning. Purchasers must obtain a projected weight of the unit that accounts for the chassis, the pump, the plumbing, the body, the tank, the water load, and any other permanently mounted equipment. Subtracting that projection from the GVWR of the chassis gives the available margin for personnel and equipment. The personnel allowance is 250 lbs for each seating position. For the common GVWR of 19,500 lbs, NFPA 1900 only requires an equipment allowance of 500 lbs if it is classified as a wildland (NFPA 1900 section 9.1). While 500 lbs might be sufficient for a barebones wildland apparatus with a basic forestry loadout, if you add supply hose, foam pails, overnight bags, hose appliances, and similar equipment, the allowance gets used up very quickly. If the apparatus has a multi-purpose role and you add SCBA’s, extrication equipment, patient handling equipment, rope rescue equipment, additional attack hose, ladders, etc – you exceed the allowance in no time at all. That’s why developing and sticking to a load plan is an important part of purchasing this type of apparatus. As reference, a similar sized structural unit will require an allowance of 1500 lbs, and that is often insufficient. Once the apparatus is ready to go into service, it should be weighed again to make sure it is not overloaded.
SPECIALTY WILDLAND APPARATUS
Mobile Water Supply Apparatus
Both NWCG and NFPA 1900 recognize wildland mobile water supply apparatus as a distinct category of wildland vehicle (Figure 13). These units may be called tankers or tenders depending on where they are located. NWCG further breaks these units into support or tactical. Support tenders (tankers) are simply water haulers. They may be structural style units pressed into wildland service, or they may be commercial water hauler units that are not necessarily purpose built as fire apparatus. Tactical tenders (tankers) have larger water tanks but also have the capability for rolling attack of the fire and must have a higher capacity pump with pump-and-roll. Regardless of the use of the unit, NFPA 1900 must be consulted as a guide for safe building practices. These units are very heavy and frequently have higher centers of gravity. Operators must be trained on their specific hazards.
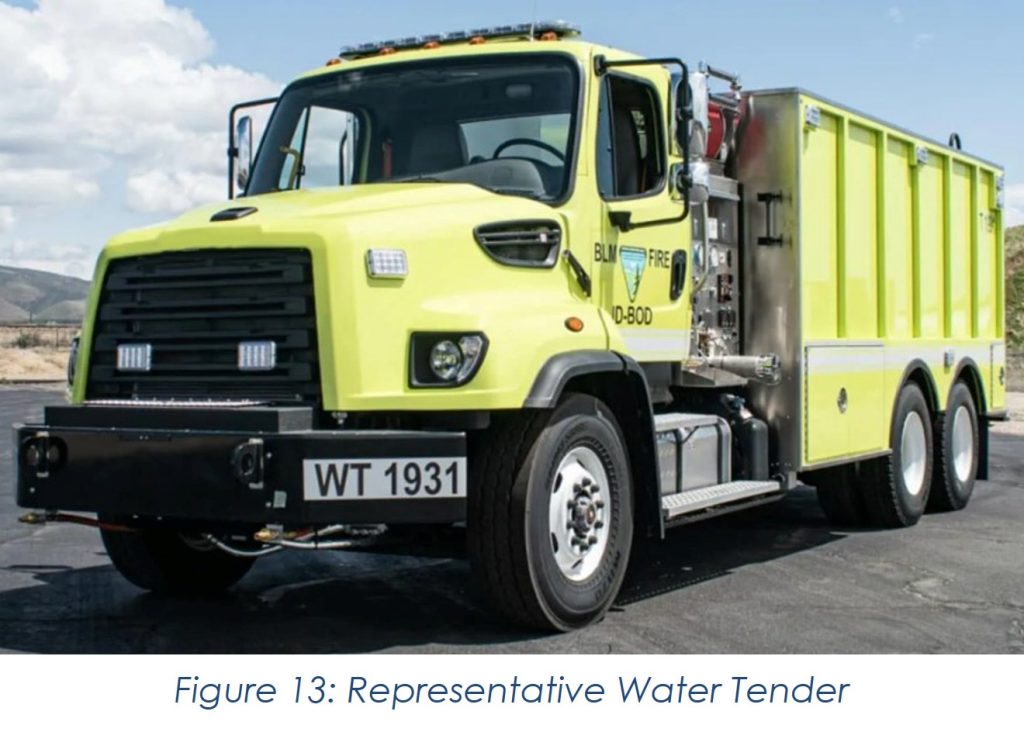
SPECIALTY WILDLAND APPARATUS (Continued)
Crew Carriers
In addition, NFPA 1900 also mentions crew carriers as a category of wildland fire apparatus (Figure 14). These units do not possess any on-board firefighting capability but are designed to transport hand crews between incidents. Some crew carriers are equipped with creature comforts for long distance travel – such as reclining seats, power ports, air conditioning, and the like. Regardless of how the unit is built, however, it must meet the structural testing requirements listed in NFPA 1900. These requirements establish a baseline performance the body is expected to meet in the event of a rollover accident. It also requires that all personnel have seatbelts to reduce the risk of injury.
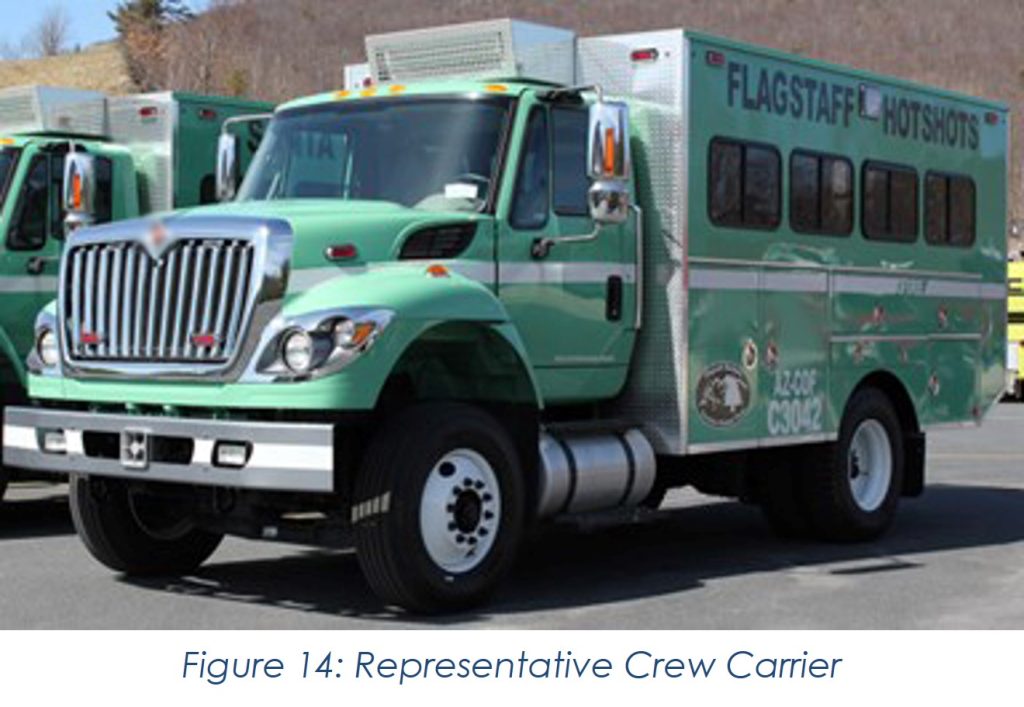
SPECIALTY COMPONENTS
What distinguishes wildland apparatus from structural apparatus? There is no one-size-fits-all answer, and both types share many characteristics. Further, since wildland apparatus range from small utility vehicles to pickup trucks to multi-thousand-gallon off-road specialty trucks, there are lots of possible options. However, there are certain types of components found more commonly on wildland units than structural units. Many of those are listed below.
ALL WHEEL DRIVE
Most wildland apparatus are equipped with all-wheel drive in one of two common arrangements. First, a transfer case is provided with a single input and two outputs. The input comes from the transmission. The outputs go to the front and rear axles with an internal shifter to engage the front axle when requested. The second method is to use a power divider incorporated into the rear axle that provides a secondary output connected to another driveline leading to the front axle. This system is sometimes referred to as a “spaghetti drive.”
The gear systems utilized for these types of systems are high torque, heavy duty design. As such, they generate heat and usually require dedicated cooling systems for the lubrication, particularly for large apparatus. They also reduce fuel efficiency and increase the service requirements on the vehicle.
More rarely, other methods may be used to provide all wheel drive, such as the use of hydraulic motors at the front wheels. In addition, there are some highly specialized all-wheel drive systems that come from military applications. These are rare, though, and usually more expensive.
All wheel drive raises the cost and complexity of the unit. Most systems also raise the height of the unit. This is not always a bad thing, as it raises the ground clearance. But it also raises the center of gravity and makes the body design more complicated. Many chassis are available with all-wheel drive options from the OEM, which reduces any warranty concerns. Occasionally, however, purchasers will opt for aftermarket conversions, which can impact warranty and eliminate single source maintenance support.
Not all wildland agencies equip their entire fleets with all-wheel drive. Some believe the typical driver may overestimate the capabilities of the vehicle. It is always possible to get an all-wheel drive vehicle stuck, and when it gets stuck, it will probably be very difficult and time consuming to get out.
SUPER SINGLES
Super singles are the installation of single tires at the rear axle(s) in place of dual tires on each side. The intent is to raise the ground clearance of the unit, provide more aggressive tire tread patterns, and to minimize the chance of the unit getting stuck due to sand or mud getting trapped between the dual tires.
There are some engineering issues to be considered. The speedometer must be adjusted to account for any differences in the wheel radius. Further, the load and speed rating of the tire must be matched to the axle. Larger tires change the torque load on the axle and driveline, which may increase the chance of damage. Lastly, such installations will raise the center-of-gravity of the unit and change the stability characteristics. If super singles are not installed by the chassis OEM, warranty and service support may be impacted.
LIFT KITS
Lift kits are used to raise the space between the axle and the frame in order to provide additional ground clearance. The additional ground clearance may be useful to allow the unit to travel over obstacles without suffering impact damage or getting hung up. Chassis OEM’s typically have limited factory installed spacers, so this space is usually filled by aftermarket kits. Aftermarket installations would not be covered by the chassis warranty. Frequently, lift kits are combined with the larger tires described above. Installation must be carefully considered because lift kits will change the stability of the stock configuration and the driveline angles.
SKID PLATES
Skid plates may be used on wildland apparatus to protect vulnerable areas under the chassis from impact during off-road travel. Areas considered for protection include engine oil pans, transmission coolers, fuel tanks, transfer cases, radiators, and steering arms. Commercial chassis OEM skid plates options are limited, so they are often added as aftermarket kits. Skid plates reduce the risk of direct impact, but do not eliminate it as the skid plates themselves may suffer damage. Skid plates should be designed so they do not trap debris or embers which could imperil the vehicle in a fire. Skid plates should also be installed so they do not prevent maintenance access or restrict cooling air flow in the radiator area.
BRUSH GUARDS
Brush guards are installed at the front of the unit to deflect objects from hitting the grille or radiator. There are lots of designs, both factory and aftermarket. The key considerations are to make sure that the brush guard does not restrict air flow to the radiator, does not prevent maintenance access (such as for tilting hoods), does not overload the front axle, and does not block the vehicle lighting. Operators should not overestimate the strength of the brush guard in off-road travel.
EMBER PROTECTION
Wildland fires may generate a large quantity of embers and ash ahead of the main body of the fire. These embers must be prevented from lodging in vulnerable areas of the vehicle. First, any embers that contact combustible items – such as items stored in the hose bed – may set the vehicle on fire. This may be overcome by hard covers over the hose bed and making sure all combustible equipment is fully enclosed. Second, debris may get sucked into air inlets for the chassis engine, the pump engine, or the HVAC system. Not only does this pose a fire risk in the filter, but an excessive buildup of debris will restrict the air flow and potentially stall the engine. All units built to NFPA require an ember separator at the engine and HVAC inlets. However, some wildland apparatus go to the next level by using fire resistant filters and making sure the air inlets are readily accessible for quick cleaning in the field to prevent clogging.
WATER FORDING CAPABILITY
Because of their off-road capabilities, some purchasers attempt to design their vehicles to travel across some depth of still or near-still water. The most critical consideration is to keep water out of the engine air inlet to prevent engine damage and stalling. For some chassis, aftermarket kits are available to raise the air intake, but their availability for all chassis is not certain. In addition, water should also be kept away from unprotected electronics and electrical components. Finally, many lubricated components such as the axles include breather tubes that should not be submerged. If water is kept out of these critical components, most apparatus can operate in some amount of water for a short amount of time. However, few apparatus are truly designed for prolonged use in water, and there may be maintenance problems weeks or even months after the exposure. Salt water in particular poses a risk for accelerated corrosion in exposed areas. If a wildland apparatus is configured for fording, then the operator must respect the limits such as the maximum allowable water depth and also follow any post-fording maintenance requirements.
FIRE WRAP
Fire wrap is the use of fire-resistant material to protect fuel lines, air lines, or electric lines on the underside of the chassis that may be damaged if the vehicle is inadvertently exposed to fires or heat in ground cover or low grasses as the unit is in motion. This wrap does not make the unit “fireproof”, nor does it prevent damage or spread of fire to non-protected components under the chassis. It simply provides an additional layer of protection for critical or vulnerable systems such as air brake lines.
FIRE CURTAINS
Fire curtains protect the cab interior against radiant heat in the event of a burnover or close exposure to flame. These can be deployed in an emergency for occupant protection. Again, these do not make the unit “fireproof”, but under certain conditions, the manufacturers of these systems say they may allow the occupants additional time for refuge while the fire front passes.
ROLLOVER PREVENTION
Users may be used to electronic stability systems that detect potentially hazardous driving conditions and adjust brakes, speed, and/or steering to prevent rollover or loss of control. However, these systems are less common in all-wheel drive units – especially large units – due to the small number of vehicles produced, the higher center-of-gravity, and the high costs of testing. Before assuming that a given chassis is equipped with such a system, ask the manufacturer. Further, even if so equipped, such systems only monitor driver inputs and skid conditions and may be less effective in reacting to events such as a shoulder collapse or shifting gravel on the road surface. Driver training will remain the primary defense to avoid these types of problems.
In addition, there are some stand-alone devices that might be useful to give some warning to the driver of potential problems. Examples include a side slope indicator or a lateral acceleration indicator that show when the vehicle reaches a pre-set side loading. Again, while these may be useful as driver tools, they are not foolproof. This is because there are a lot of variables that determine when a unit is close to tipping over, and these tools can only show one or two of them.
AIR BAGS AND SIDE ROLL PROTECTION
Airbags are commonly available in two types – frontal impact and rollover / side protection. These are generally available as factory installations for small apparatus but are rarely available for large commercial apparatus except as an aftermarket addition. Related, part of a side roll protection system may include safety seats. These systems sense an imminent rollover and immediately pretension the seatbelt and lower the seat to the lowest travel height. This helps secure the occupant and position them to minimize the chance of injury and maximize the effectiveness of any airbags. Availability must be confirmed with the specific builder.
ROLL CAGES AND IMPACT PROTECTION
Some vehicles may be equipped with brush cages designed to prevent tree branches or other offroad obstacles from hitting vulnerable parts of the unit during travel. The areas commonly protected include the windshield, the fenders, and the rear cab window. These may be installed simply on the sides or front of the cab or body, or they may envelope the entire cab. You may sometimes hear them referred to as “roll cages”, though this is a tricky and potentially misleading term. A roll cage is designed to prevent the cab from being crushed in the event of a rollover accident (see below). A brush cage or window protector should not be confused with a roll cage or roll bar.
Roll cages are systems of internal or external cab reinforcement designed to prevent the cab from being crushed into the occupant space during a rollover. These are rare. For all cabs, the cab itself will be designed to meet certain industry standards for cab integrity and occupant protection. However, the tests for these standards are partially static and may not fully replicate the real-world conditions of a rollover. Further, the amount of extra margin in resisting crush will vary by chassis model. Real world experience has shown that while custom designed apparatus cabs tend to have a larger margin, some commercially available cabs have little extra margin. To that end, users may request additional protection via roll cages. If a user wishes to specify this type of protection, then it is critical that they ask about the basis of the design. Without simulation and testing, the effectiveness of the system may be limited.
Lastly, some builders or purchasers raise the height of the front of the body or install a body mounted rollbar style assembly to match the height of the cab so that it provides additional protection to the cab in a rollover. In general, the body has more structural integrity than the typical cab, and some real-world accidents have shown this is favorable. But the presumed effectiveness of such designs in a rollover may be untested and should not be overestimated.
PUMP-AND-ROLL
Pump-and-roll is the ability to maintain a flow of water from the pump system while the apparatus is moving. It is not the same as simply being able to keep the pump in gear while in motion. The flow of water must be of sufficient size and pressure to conduct rolling fire attack. NFPA 1900 specifically defines the minimum pump-and-roll performance as 20 gpm at 80 psi at 2 mph (NFPA 1900 section 15.2.2.1). NFPA does allow the operator to use both the foot brake and the foot throttle simultaneously to raise engine and pump RPM while restricting travel speed. However, this can be tricky in practice and easily results in “bouncing” on the throttle with the resulting spikes in pump pressure. The most effective pump-and-roll systems control the pump pressure independently from the chassis engine RPM.
In addition, the truck must be equipped with appliances by which the water is applied – a hose reel, a whip line, ground sprays, or turret. See below for those items.
For maximum pump-and-roll effectiveness, users should consider having the ability to control the pump from inside the cab, including a remote gauge to monitor pressure. Some pump systems are better suited to this than others (see the pump section).
HOSEREELS
Almost every wildland apparatus will be equipped with at least one hose reel. The reel provides three advantages over soft line. First, the semi-rigid hose allows the operator to quickly deploy “just enough” hose length to attack the fire. And when the operation is complete, it allows rapid storage of the hose to get on to the next thing. Second, the size and length of the hose is well suited for low flow operations. Most wildland attack nozzles have ratings below 30 gpm, Third, depending on the hose, the hose remains relatively light while the exterior jacket may resist snagging or damage when being pulled through brush, rocks, and gravel.
Ease-of-use should be the main consideration in mounting the hose reel. Small apparatus are often low enough that the reel can be mounted on the top of the water tank or at the rear of the body without reducing other compartmentation. Popular locations for large apparatus are in the rear compartment, over the pump module, or in pockets on the side of the body. In some types of chassis, storage may be available under the cab, but that space is increasingly reserved for emissions aftertreatment components that cannot be relocated. In all cases, the size of the reel is defined by the length, diameter, and type of hose required. Reels for 125’ to 150’ of 1” hose are common. Larger reels require more planning. The rewind activation should be positioned to free at least one hand to guide the hose onto the reel via rollers. And a nozzle bracket will be useful for quick deployment while positioning the hose to avoid getting snagged by trees or brush while traveling.
GROUND SPRAYS
Ground sprays provide a flow of water under, in front or, or to the sides of the vehicle to dampen down hot spots near the vehicle during travel. They may be useful for rolling attack, for mop up operations, or to simply keep the dust down on unpaved roads.
TURRETS
Some wildland apparatus will be equipped with a remote-controlled water turret that allows water flow to be aimed at the fire from inside the cab. This may minimize the need for someone to walk alongside the unit, and it may prevent the temptation to ride outside the cab.
ENGINE PROTECTION LINES / WHIP LINES
Some units are equipped with readily accessible short sections of hose that the operator can quickly deploy to protect the engine against embers or spot fires in the immediate vicinity of the unit. Such positions will include a small storage bin for the hose and nozzle and a locally controlled valve for quick operation.
WATER CURTAINS
Water curtains or spray systems provide a flow of water over the top of the vehicle to minimize damage if the unit gets too close to the fire or becomes involved in a near burnover situation. The effectiveness of such systems is rarely tested and is likely unpredictable based on the actual conditions – available water volume, fire intensity, and air quality at the pump engine. Because of these variables, they are not common.
EXTERIOR ATTACK POSITIONS
In certain locations in some types of terrain, some departments find it useful to conduct a rolling attack with firefighters riding on the unit using a short handline to sweep the fire and knock it down quickly. However, users of these types of apparatus must carefully consider the safety risk to those firefighters. Rolling attack presents risks in terms of rollover protection, ejection from the vehicle, and foreign object impact. For such positions, the NFPA 1900 annex provides guidance on how such a position could be constructed (NFPA 1900 A11.1.1).
FOAM OR GEL SYSTEMS
To maximize the effectiveness of the limited available water, many wildland apparatus are equipped with Class A foam. This foam acts as a wetting agent allowing it to penetrate deeper into the fuel to reach the seat of the fire. It also provides a blanket that may delay reignition, even if it is exposed to further heat. There are two primary methods to inject the foam. Eductors use water flow to create a suction that draws the concentrate into the stream – simple, but generally less accurate and consistent than other methods. More typically, a small motor driven injection pump is used to match foam concentrate to the water flow.
Compressed Air Foam Systems (CAFS) go one step further and inject air into the foam solution so that foam bubbles are created in the hose line rather than at the nozzle. This lowers the weight of the hose and allows the consistency of the foam to be adjusted from wet to dry. Wet foam has better surface penetration. Drier foam lingers and provides exposure protection. In addition to the foam injection portion described above, these systems require a balanced air injection system. Less expensive systems may use stored air cylinders. More complex ones use compressors attached to the pump drive system. Both add complexity and weight.
Gel systems are like foam systems in that they act as wetting agents making the water more effective in reaching the seat of the fire and preventing reignition. However, they do not require air injection into the stream as part of the chemistry. The injection rates will vary from Class A foam, and the viscosity of the gel will likely require larger injection systems and more space on the apparatus.
ULTRA HIGH PRESSURE PUMPS
Ultra high pressure pumps are pumps that provide discharge pressures in excess of 1100 psi. Due to the pressure, these are lower flow systems – less than 10-20 gpm per handline. The makers of these systems indicate that the high energy in the system divides the spray into smaller droplets that are more effective at absorbing heat than lower pressure systems. This makes the water more effective at a lower flow, so less water is used. The higher velocity leaving the nozzle will also penetrate deeper into the fuel making it more likely to reach deep seated fires.
FLEXIBLE BODY MOUNTING
In order to minimize the stress transfer from the chassis to the body while the unit is traveling in rough terrain, many wildland apparatus incorporate flexible body mounting that allows the body to lift slightly away from the chassis frame. This helps minimize the twisting that goes into the body and prevent body damage or cracking.
SPARE TIRE STORAGE
Because wildland apparatus can operate for prolonged periods in remote areas, some wildland apparatus carry a spare tire. The design challenge is that tires are large and bulky. If spare tire storage is required, frequently it is a tradeoff between storage for other equipment and ready access to the tire. There are some creative solutions on the market, including dedicated compartments with powered winches and gantries, but more commonly – particularly for small apparatus – the tire may simply be stored on top of the water tank. In all cases, the tire should be secured to the unit while in transit, and the crew should preplan how the tire will be removed and restowed in the field.
HARD HOSEBED COVERS
Many wildland apparatus include hard covers over hosebeds and other storage areas. This provides two advantages. First, as mentioned previously, the covers are non-combustible and prevent embers from accumulating in the hose bed area. Second, they provide a flat, slip resistant walking surface if the crew must operate on top of the unit. If designed as a walking surface, the cover should meet NFPA 1900 section 12.6.
WINCHES
Many wildland apparatus will be equipped with a winch. Small electric winches with a capacity of up to 15,000 lbs of pulling force are most common. Smaller portable winches are also available that can be positioned in receivers at the front, rear, or sides of the unit. Winches may be used to assist in self-recovery if the unit becomes stuck. They are also used as stabilization tools in rescue situations for multi-purpose apparatus. NFPA 1900 chapter 24 provides additional requirements for winch installation.
INTERFACE ZONE HOSE STORAGE (I-ZONE BRACKETS)
In the interface zone, apparatus often need to reposition quickly while moving between structures for exposure protection and fire attack. In such cases, the unit may have lengths of attack hose deployed that need to be quickly gathered before the apparatus is moved. I-Zone brackets are hook-like attachments on the vehicle that hold the hose for short, low-speed movements. They are for temporary storage only and are not suitable for securing the hose during on-road travel to and from the incident.
BODY STORAGE
Because of their use off road, most wildland apparatus purchasers will agree to limited storage to minimize the overall size of the vehicle. Of course, the size of the storage spaces must be tailored to the apparatus purpose.
Some of the considerations for storage are as follows:
- A storage plan is important for all fire apparatus, structural or wildland. As noted in many places in this document, a large body reduces the mobility of a unit. While there is no formal length measurement that makes a unit ineffective, there are some guidelines that can be seen in common usage:
- OAL (Small Apparatus): 20’ to 25’
- OAL (Large Apparatus): 25’ to 28’
- Bear in mind that since most wildland apparatus are mounted on engine-forward commercial chassis, most of that length is taken by the cab, especially for a crew cab. What’s left can be used for the body and pump. Preplanning what tools are to be carried in the available space is a critical tool for making sure the size is optimized as much as possible between maneuverability and function.
- Many wildland tools have long handles and wide heads – shovels, rakes, brooms, and the like. Dedicated, accessible storage should be provided.
- Gasoline powered handtools – blowers, chainsaws, etc – are not uncommon for wildland units. In addition, some crews carry liquid fuel drip torches. Isolated storage for these items and the fuel may be useful. Such storage should be vented and isolated to prevent contamination of other equipment. Straps, brackets, and spill trays are recommended to prevent spills and facilitate cleanup.
- If the unit is expected to carry ladders, the purchaser will have to make some decisions. Short, 3-section extension ladders (16’ or 20’) are available that will fit in a short body (8.5’ to 9’.) Longer ladders – such as would be expected on a pumper – will either require a longer body or external storage. This may have a cascade effect to increase the overall size of the unit. If ladders are to be carried, these should be considered from the beginning so the body package may be configured accordingly, and the ladders do not become an afterthought.
MATERIALS
Just like with other types of fire apparatus, there are several materials to choose from when it comes to the construction of wildland apparatus bodies and compartments. The following gives advantages and disadvantages of each specific material for body construction:
GALVANNEAL STEEL
Advantages: Strong, inexpensive, very durable, less prone to cracking
Disadvantages: Heavy, more prone to corrosion (requires paint or similar coating process)
STAINLESS STEEL
Advantages: Strong, good resistance to corrosion, does not require paint
Disadvantages: Heavy, higher material cost, more difficult to weld
ALUMINUM
Advantages: Lightweight, does not require paint, can be extruded into custom shapes
Disadvantages: More expensive (can be offset if not painted), requires skilled welding and repair, subject to ductile fatigue failure
COMPOSITE
Advantages: Lightweight (can be significantly lighter), flexible, does not corrode or rust
Disadvantages: Requires UV protection, limited manufacturers can fabricate, limited body designs as the body must be constructed from a mold
THERMOPLASTIC*
Advantages: Does not corrode or rust, flexible, reasonably lightweight, can be integrated with water tank for maximum storage in minimum space, impact resistant
Disadvantages: May warp or melt when exposed to very high heat, limited fabrication and repair facilities
*The exact formulation and performance of the plastic will vary by manufacturer, but the two most used plastic types are polypropylene and polyethylene.
PUMPS
Wildland pumps differ from structural pumps in three ways:
- Almost every wildland apparatus is designed for pump-and-roll, meaning that you need volume and pressure sufficient for fire attack at relatively low travel speeds. (Minimum 20 gpm @ 80 psi @ 2 mph)
- Wildland pumps are defined by NFPA 1900 as having a rating of 250 gpm or below. Unlike structural fire pumps, the pressure rating is variable from 100 psi to 400 psi depending on the volume rating (NFPA 1900 Chapter 15). Structural pumps, in contrast, are always rated at 150 psi from draft.
- A small wildland pump system can be a simple installation, with basic valves, drains, gauges, and manifolds. The breakover point is 250 gpm, above which the pump is required to have all the “bells-and-whistles” of a structural rig. This includes specified controls at the pump panel, line gauges for individual discharges, line drains, etc. This requires careful planning when installing larger pumps on a wildland apparatus (see below).
In general, dedicated pump-and-roll wildland pumps may be driven as follows:
Separate Engine Driven (Gas or Diesel)
- Advantages: Best pump-and-roll performance (pump is truly independent of chassis speed); pump engine provides redundancy versus pumps driven by chassis engine; ideal for smaller pumps
- Disadvantages: Take up more space and weight compared to chassis driven pumps; higher pump ratings require significantly larger and heavier engines; more complex to provide remote actuation and pressure control
Transmission or Engine Power-Take-Off (PTO) Driven
- Advantages: Cheaper and lighter to buy a PTO versus a separate engine; more horsepower available for larger flow and pressure ratings; easy to actuate from inside the cab
- Disadvantages: The higher the pump rating, the less consistent the flow during pump-and-roll. Small variations in engine speed while driving can create large fluctuations in discharge pressure.
Hydraulic
- Advantages: Good pump-and-roll because the hydraulic system can smooth out the pump performance relative to engine speed.
- Disadvantages: More complex, more expensive; requires hydraulic reservoir; not easily scalable for larger flow ratings; limited manufacturers
STRUCTURAL PUMPS
As noted above, some larger wildland interface units will also include a higher capacity (≥ 750 gpm) structural fire pump. If purchasing an apparatus so equipped, consider the following:
- Most structural fire pumps are split shaft driven. Because such pumps are installed in the driveline, they are limited to stationary pumping and cannot perform pump-and-roll. If pump-and-roll is required, a separate pump must be provided for this purpose. The pump-and-roll plumbing may be standalone or may be integrated into a common piping system with the structural fire pump.
- For split-shaft pumps installed on all-wheel drive chassis, the pump gearbox will compete for space with the all-wheel drive system. This will result in longer wheelbases and/or higher pump installations to keep the drivelines aligned.
- The most common all-wheel drive transfer case used on large apparatus is available with its own PTO output. This output can drive a pump with a rating up to 1500 gpm and eliminates the need to split the driveline again, thus limiting the need for a longer wheelbase. Such installations still function like split-shaft pumps and are only capable of stationary pumping.
- As noted above, transmission-driven PTO pumps can stay engaged while moving. For large apparatus, it is possible to provide an NFPA pump rating up to 1500 gpm. However, as the rating increases, the low-end performance decreases, and the actual performance may be insufficient for pump-and-roll attack at low speeds. Multistage or multi-impeller pump setups can solve this problem but will require additional space with more complex plumbing. If the user wants to use a larger PTO driven pump for pump-and-roll, verify the expected low speed performance will still meet the required performance.
Conclusion
This document serves as a high-level overview of wildland fire apparatus. Many FAMA member companies produce wildland apparatus and can be great sources of information with more detail. If you have questions, please do not hesitate to contact any of the companies listed at www.fama.org/members/list/.