PLEASE NOTE: the member portal is under maintenance
Equipment Mounting – Body
FAMA BUYER’S GUIDE TC058 Equipment Mounting – Body
Equipment Mounting – Body
Prepared by the FAMA Body Subcommittee
This guide does not endorse any manufacturer or product
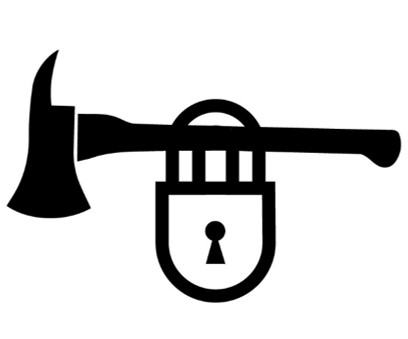
Contents
Introduction
Tool and equipment mounting and organization are often overlooked when purchasing a truck or putting a truck into service.
This buyer’s guide looks at enhancing the performance of your department, while protecting tools and equipment by properly mounting them. This can be achieved by making tool mounting decisions earlier in the budget and truck planning processes.
Overview
This guide, Equipment Mounting – Body, includes segments as shown in the table of contents. Background material, advice and information is provided by FAMA Industry representatives. Contact component and apparatus manufacturers for more information and what options are available. Manufacturers can be found in the Manufacturers Guide at www.fama.org. Products shown are for example only, and no specific brands are endorsed.
Uniformity
Uniformity is the practice of organizing tools on different trucks in the same manner. Many departments use this as a policy to improve performance at the emergency scene.
Fire departments may have several types of apparatus, possibly spread over many stations. When tools and equipment are mounted in the same locations on every truck, it will allow personnel to know exactly which compartment has the item they are retrieving, for example, the Storz adapters or the bolt cutters. Mounting tools uniformly removes the guesswork and “hunting” for the item needed.
Accountability & Preservation
With uniform mounting locations, it is also important to know what tools or equipment should be located in a particular location. It is also a good practice that each mounting location be labeled. That will assist in knowing at a glance what items may be missing, so that they can be located and secured before leaving the scene. If items do not have a proper mounting location, they can be left behind at a scene, mistakenly placed in another compartment or taken by another responding company. By properly labeling every location, inventory can be quickly surveyed after each scene, ensuring tools have been returned to their proper storage location. When a truck is at the station it can be quickly surveyed for missing equipment.
Additionally, properly secured tools, will be much less prone to damage that is caused when tools are simply tossed into a compartment with other items. This accountability keeps mounted tools in working order, avoids them from being thrown around in a compartment, and will keep them ready for the next use. This will preserve tools and can reduce overall operating costs.
Another issue with unsecured tools is when larger equipment falls against the inside of a roll-up door. This causes an avoidable situation where the door cannot be safely rolled up, losing critical response time.

Safety Concerns
According to NFPA’s “U.S. Firefighter Injuries – 2015”:
- There were an estimated 16,600 collisions involving fire department emergency vehicles responding to or returning from incidents. This is the highest number of collisions since NFPA began collecting this information in 1990.
- 68,085 firefighter injuries were reported in the U.S in 2015. Of these, 29,130 were injuries at the fireground.
Every agency must reduce hazards to prevent injuries from happening. Tools and equipment should not fall out of compartments when the door is opened – this is a preventable hazard! Falling equipment and tools have caused severe injuries and have needlessly taken emergency responders out of service. Avoid injuries by organizing and securing your tools.
NFPA
The National Fire Protection Association (NFPA) has both requirements and guidelines regarding tool mounting on fire apparatus. These were written to protect the public as well as the firefighters.
NFPA standards were drafted in light of data collected from the high number of collisions and rollovers involving fire apparatus. To be NFPA compliant, the standard requires manufacturers to perform tests that replicate high G-forces generated in a rollover incident. Another NFPA requirement covers all loose tools transported in a crew cab.
NFPA 1901 and 1906 Standards contain lists of the minimum equipment for various apparatus types. It is the Fire Department’s responsibility to identify who is to supply and mount the required minimum equipment and to ensure that it is completed prior to putting the apparatus in service.
The apparatus manufacturers deliver NFPA compliant apparatus. When a department loads equipment onto an apparatus, the apparatus may become “noncompliant”.
Chapter 15, Body, Compartments, and Equipment Mounting should be referenced. Section 15.3 shows the requirements for Equipment Containment.
Corrosion
Corrosion is generally thought of as simply rust, as in the oxidizing of steel. Dissimilar metals in contact with one another can react and cause galvanic corrosion. A steel bracket on an aluminum body (or vice versa) will lead to galvanic corrosion. The oxidation will then permeate from the contact zone, ruining paint or weakening bodywork. Unsightly pitting can become visible on the once shiny, smooth surface.
Damage can be avoided by selecting corrosion free tool mounting brackets or by adding insulation material in the contact zone.
Fluids and Chemical Resistance
A selection of well-maintained rescue equipment on your apparatus significantly contributes to your Department’s performance. To keep these life-saving machines operating on scene, you must allocate extra space in the apparatus. In addition to tools for maintenance, or extra saw blades, it is often necessary to carry fuel and lubrication. These fluids are often toxic, flammable, caustic and corrosive.
Select holders and pockets where these fluids can be stored upright, safely and securely. Holders and pockets should be chemical-resistant as well.
Chain saws, rescue saws and other powered equipment may leak fluids that will pool below them. Special tiles and pads are available to prevent oil from coming in contact with skin and PPE. Planning properly for storage of fluid using machines also prevents chemicals from coming in contact with parts of the apparatus, or other loose equipment, that may not be chemical resistant.
Wall-Mounted Tool Boards
A wall-mounted tool board brings secure storage to a bare compartment. Most often these are considered optional equipment by apparatus manufacturers.
Several manufacturers (OEM and aftermarket) offer tool boards for wall mounting. Each tool board product has functional differences. Not only material or weight differences but more importantly the way the boards attach to the compartment and the way brackets are attached to the boards.
A wall-mounted tool board can offer these advantages to your agency:
- Tool boards allow quick mounting of brackets or clips to secure tools.
- Get the delivered Apparatus in service faster!
- Easily rearrange brackets to maximize storage space.
- Rearrange again, at a later date, to include new tools or to repurpose the truck.
- Prevent additional or unnecessary drilling in your new compartment.
- Avoid potentially expensive electrical or plumbing issues when adding holes to compartment walls.
To minimize the time to get your new Apparatus in service, wall-mounted tool boards should be in the truck specification.
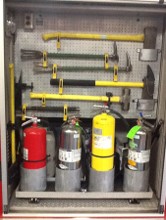
Slide-Out / Swing-Out Tool Boards
Sharing some of the same attachment elements, and features as a wall-mounted board, slide-out and swing-out tool boards add more storage area to a compartment. Usually these are considered optional equipment by OEMs.
On some trucks, or with larger equipment, these types of tool boards are necessary to properly and safely store equipment. A slide-out tool board can offer these advantages to your department:
- High or tall compartments (over the wheel well, for instance) put tools out of reach.
- Generators and pumps can be lifted off a horizontal slide much easier than pulled out of a compartment.
To minimize the time to get your new Apparatus in service, slide-out and swing-out tool boards should be in the truck specification.
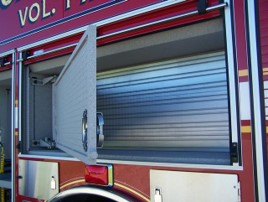
Pocket Style Tool Mounts
This section looks at the most basic tool mounting component: POCKETS. Pockets can be small or large. Pockets can be constructed of plastic or metal with paint or powder coating. Some pockets are formed, while others are fashioned by welding plastic into shape.
Whatever the construction, the function is the same: provide a place for a tool to be dropped into it.
Pockets have some limitations:
- By itself a pocket does not provide a restraint to keep the tool in place during transit or a crash incident.
- A pocket does not provide protection to a crew member that may come in contact with exposed points, blades or other sharp edges.
- To secure larger tools, such as axes and sledge hammers, additional brackets (friction or positive locking) will be required.
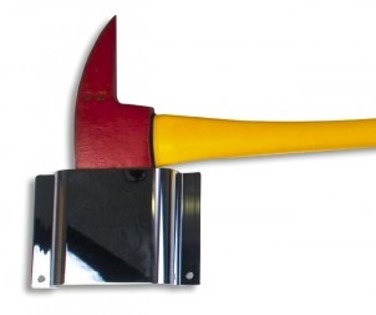
Friction Tool Mounts
The simplest type of mounting bracket is the friction type. To store tools in these brackets, the user pushes the tool into the bracket. To release the tool from the brackets, the user pulls the tool until it releases.
Considerations when choosing friction mounting brackets:
- Selecting a bracket that has the proper grip range is paramount; too big and the tool will be loose and could fall out unexpectedly…
- Products are not locked in.
- Over the life of the product, the strength of the grip may become reduced.
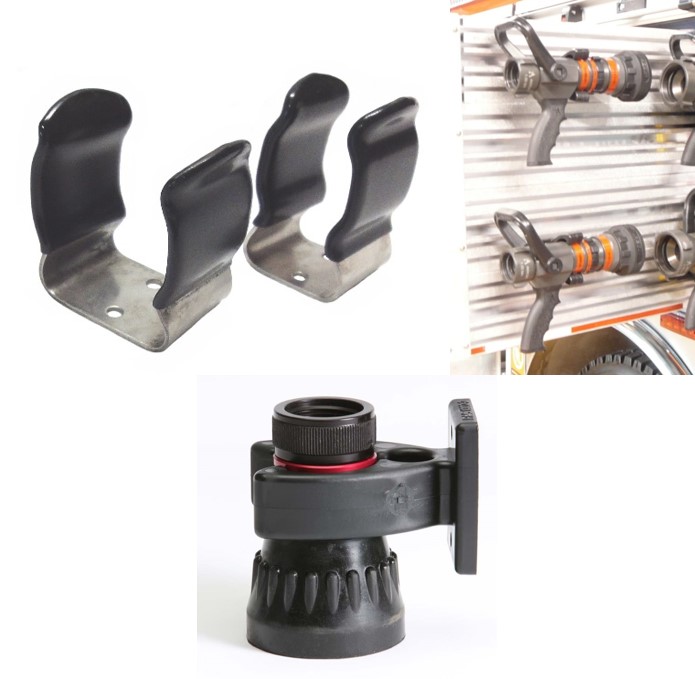
Positive Locking Tool Mounts
Unlike friction tool mounts, positive locking tool mounts retain tools until manually released by the user. Components usually include a rigid base and a separate strap member. The strap member may be an elastic material or it may be a nylon strapping with a common buckle (like on a lifejacket).
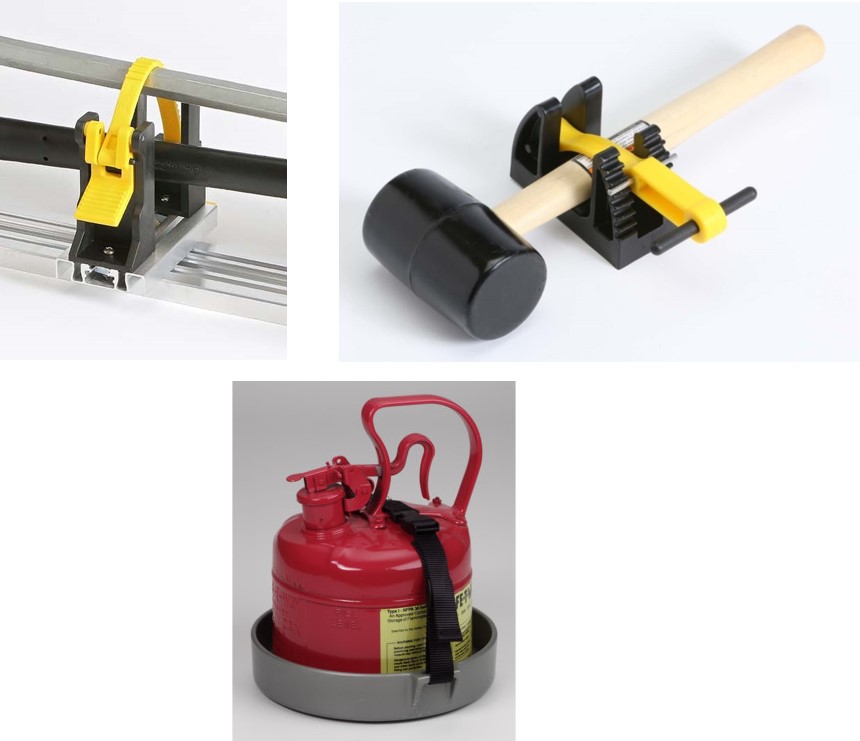
Adjustable Grip Range Tool Mounts
Tool mounting brackets with adjustable grip range allow the user to change the usable dimensions. Rescue Tools, for instance, undergo design changes over time. When replacing an expensive rescue tool with a newer model, having an adjustable tool mounting bracket minimizes the downtime of your apparatus as the tool compartment gets overhauled.
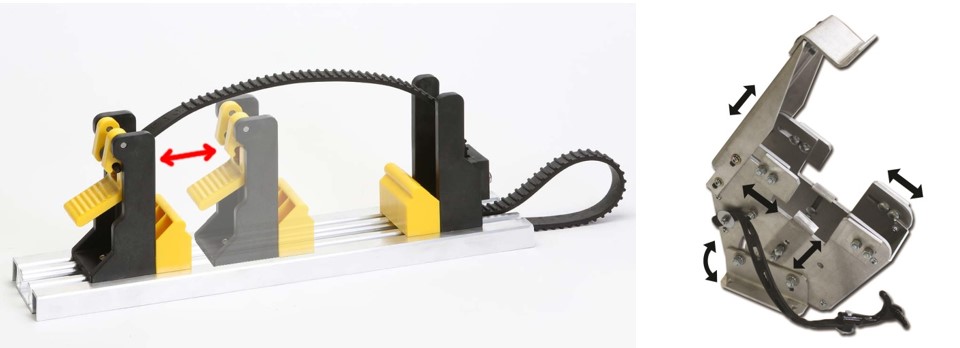
Exterior Mounting
Exterior vehicle mounting of tools must be carefully considered. When deciding which tools will be outside the truck, you should consider:
- Safety – of the crew and the public – when a tool is unexpectedly liberated.
- Loss – tools may fall off the truck; avoid costly replacement expenses.
- Theft – if your truck is stored outside, externally mounted tools may be stolen!
- Weather – UV will affect the integrity of tools and tool mounting brackets; select UV resistant materials whenever possible.
SCBA Cylinders
Spare air (SCBA) tanks can be stored in the body of an apparatus. One issue with air cylinders is the varying diameter and length due to manufacturer, material or capacity. When purchasing a new truck: take care to specify the proper compartment depth to accommodate your cylinders. Specify a depth that can hold the intended cylinder and/or the mounting assembly. The manufacturer can provide overall dimensions.

SCBA Cylinders (continued)
OEMs offer cylinder mounting above wheel wells (in the void area above the tires) and closure is made with a door.
Additional cylinders can be mounted in the truck compartments (with proper depth behind the door). Aftermarket products range from simple grids to single locking enclosures.
SCBAs carry a high dollar value. A damaged cylinder valve is a dangerous hazard – cylinders can become projectiles! Also, the cylinder construction itself may be compromised due to wear and abrasion rendering it unsafe to be used in service. Protect the public, your equipment and your department’s budget by securely mounting your cylinders.
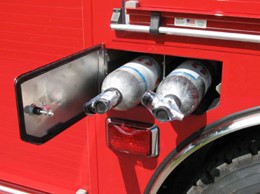